How to forge a career in blacksmithing
Skills | Written by: Fiona Kantzidis | Thursday 9 January 2025
If you’re thinking of training as a blacksmith, or know someone that might be interested, read on to hear from our amazing Blacksmithing Craft Fellow, Murray Holmes, based at Ratho Byres Forge.
In Scotland, blacksmiths create, conserve and maintain historical ironwork. Blacksmiths do small things that make a big difference and lots of work and energy goes into their craft that people don’t get to see.
It is quite a diverse trade, including fabricator and welder roles, but fabricating and welding are different type of blacksmithing from the kind we need to maintain and decorate historic buildings and structures. Some specialisms within blacksmithing are thriving while others have limited numbers of practitioners. It is important that we preserve these traditional skills so repairs and maintenance are done right – badly done repairs can do more harm than good.
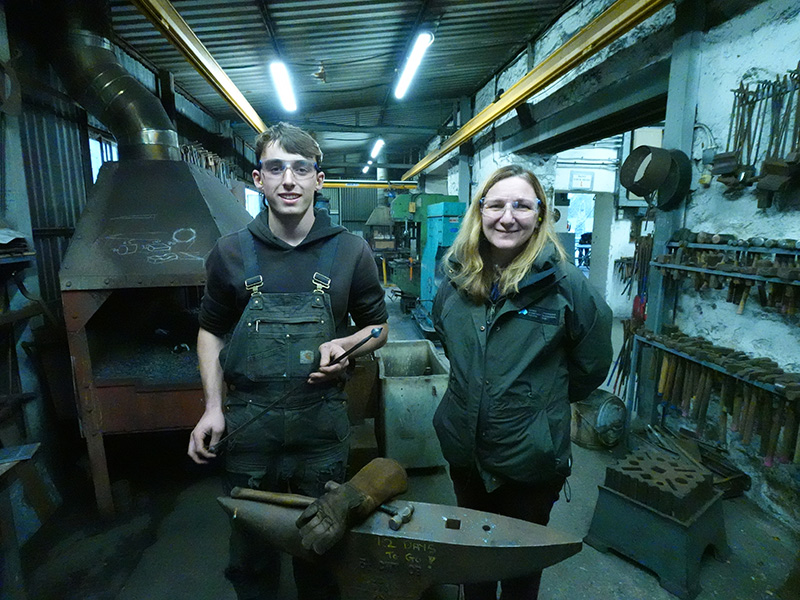
Murray Holmes, our Blacksmithing Craft Fellow (left) holding a leaf point he made and Fiona Kantzidis, our Technical Conservation Skills Officer (right) at Ratho Byres Forge.
Murray, how did you discover blacksmithing?
I did my school work experience at Ratho Byres Forge, managed by Pete Hill and Shona Johnson. My work experience was only supposed to be two and a half months, but I kept asking to come back! So it ran through the summer and then I found that I had still been here after a year.
Update your personalised ad preferences to view content
Before I started my craft fellowship, I met Vicky, who trained with Historic Environment Scotland as a blacksmith about nine years ago. There is a video on YouTube about Vicky’s personal project, so I knew there had been trainees before. I then just emailed Historic Environment Scotland (HES) as I didn’t know that you usually apply for a job as a Craft Fellow when they are posted on HES vacancies!
School careers guidance staff kept sending me applications for fabrication jobs, but I didn’t want to do that. They didn’t really get the blacksmithing thing.
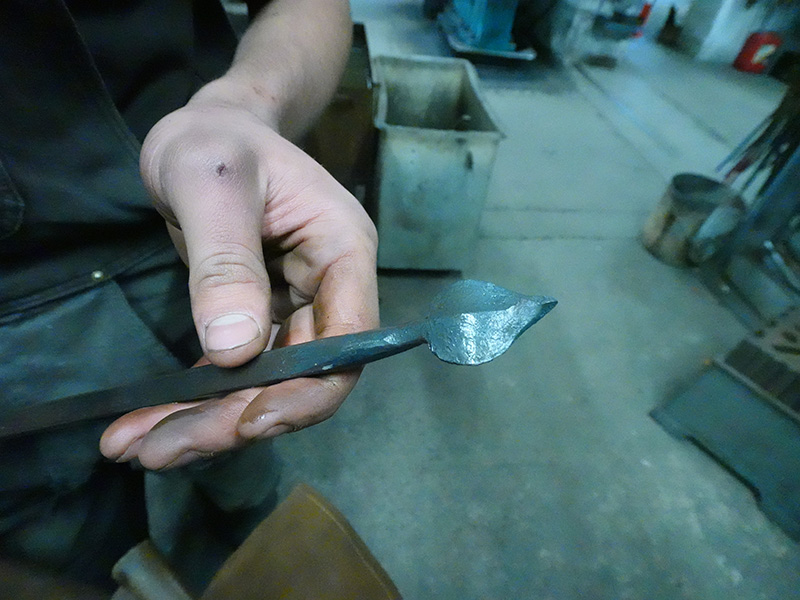
Murray holding a leaf point he made, taking only minutes, at Ratho Byres Forge.
How would you describe your job in three words?
Blacksmithing is definitely intense. It works in stages where one minute there is a lot of head scratching and then it can move forward quickly in the forge. The best bit of the job is when you are working on a piece all day and you get to see it progress over time. It is quite fulfilling. You also have to be very creative and you are definitely always learning. Pete and Sheona have been doing this for so long, but as no two jobs are the same, you have to be creative in the way you go about things for each job.
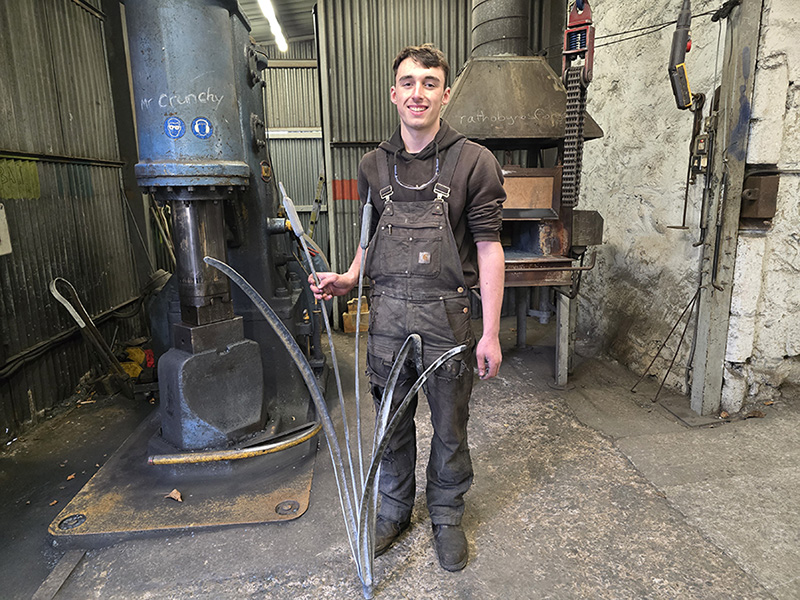
Murray holding a metal bulrush (or reedmace) piece he has been working on.
What kind of things have you made at the forge?
I’ve made quite a few things now, including a bird. I had one project that was out of my comfort zone, this was when a family friend asked for a dragonfly piece for their pond. I made it with help from the others at Ratho. The dragonfly’s wings were an 8mm round bar, all very intricate and tig-welded with every little bit filed round and taking quite a while. The body was forged out of pipe, a completely different ball game and a challenge to forge as pipe wants to collapse in on itself. Pete made a 3D model of the dragonfly in cardboard and we dangled it over the pond with a fishing rod to see if it was the right size.
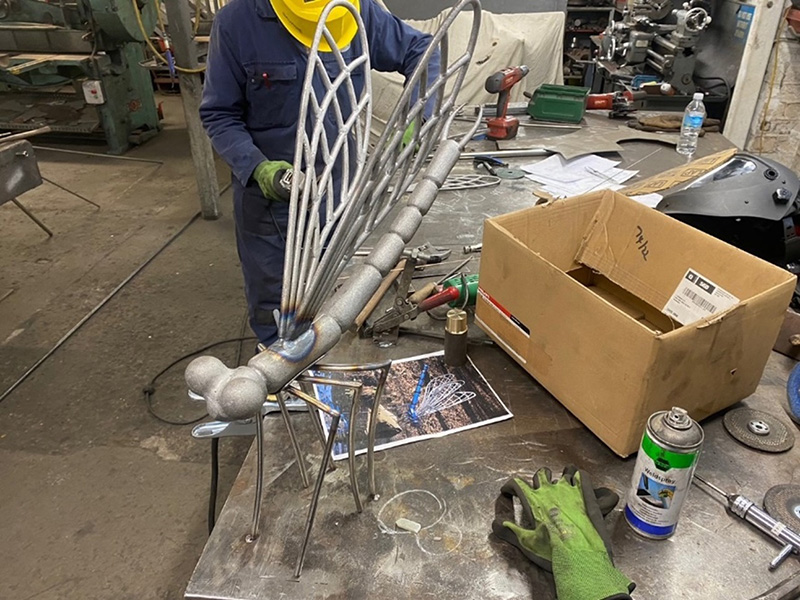
Murray’s dragonfly piece during construction. © Murray Holmes.
Have you passed on your skills to others?
I do a bit of boatbuilding with a builder down in England, including a bit of hot-riveting, welding, woodworking and work on engines. It’s not forge work, but we had to make these tiny little hooks for strings to hold the caulks (a material used to seal joints) down. For such a simple thing, it was a nightmare to make. The hook we used as a template to replicate from was from the 19th century, I think, and he needed new ones. I showed him the fire-welding and used a gas-torch, which slows down the process. We made dozens of the hooks in the end for his stock.
Have you ever worked on a HES property?
For Ratho, I worked on shot-blasting railings for Edinburgh Castle esplanade. Shot-blasting takes the railings back to the metal and is part of the refurbishment process.
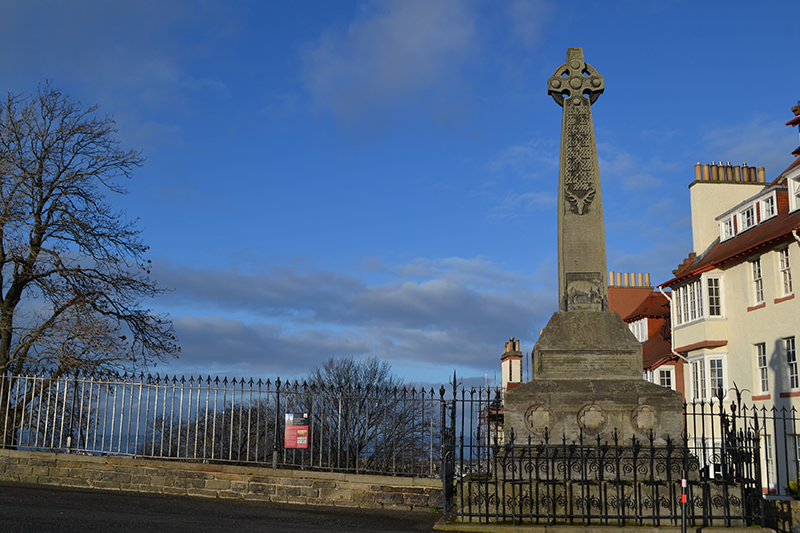
View of the India Cross showing railings behind it, on the esplanade at Edinburgh Castle.
What would 5 year old you think of your job?
I was quite the old man as a kid, putting my flat cap on and going down the harbour with my grandad, like a proper old man child. It probably wouldn’t have surprised me that I do this. My grandad was an engineer, so I was always helping him in the shed.
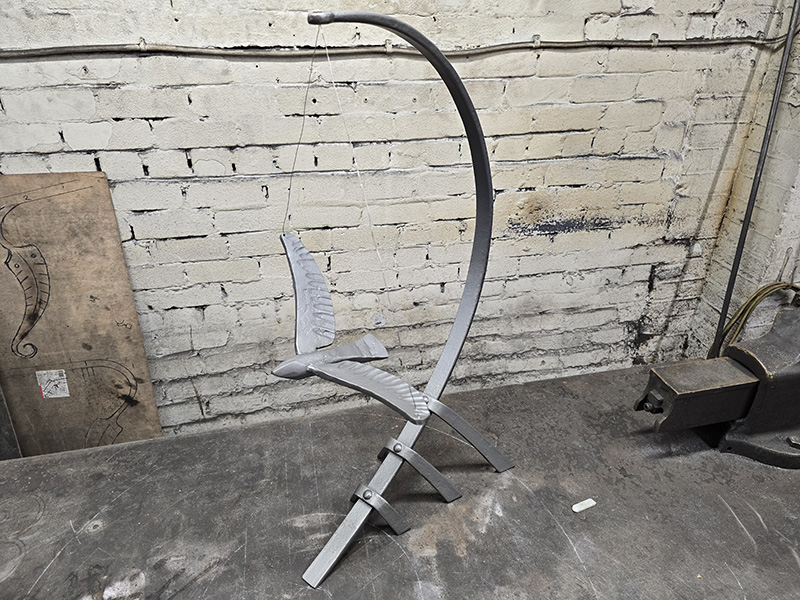
Murray’s piece here is a bird in flight, during construction, held in place with some temporary wire.
What do you enjoy most about your role?
Probably working with so many different people. As Ratho Byres Forge is one of the biggest firms in the country, I’ve seen so many ways of working. Everyone figures out their own way of doing things over the years. This place is a bubble where everyone knows each other so well and is willing to share knowledge and ideas. Even outside of the forge, Pete and Sheona have friends who visit to chat and share advice. The community in it means it never seems to me to be a competition. There is enough work for everyone, as long as you go about it the right way.
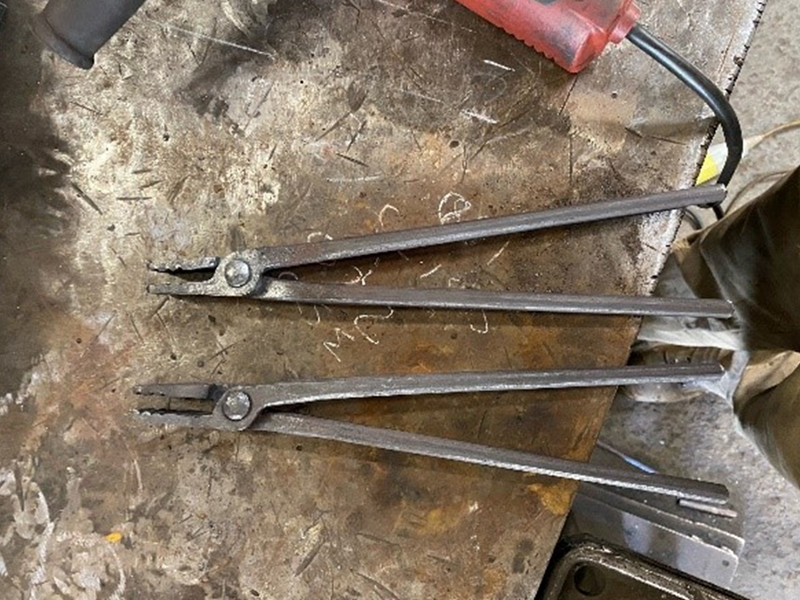
Murray’s pair of tongs made using traditional blacksmithing skills. © Murray Holmes.
So, what is next for you?
Design is not my strong point. I can picture things in my head but putting it onto paper is where I struggle. When I finish up here, I plan on doing as much forge work as I can, and I have looked at railing jobs. I’d love to be able to draw something like Pete and Sheona can, which comes from years and years of experience. As they say, the best way to learn is to get a pencil and paper and just draw. There is a course in Hereford, where you learn technical skills and forging, though I have done that here. The rest of the course is artists blacksmithing, which is learning design and how to put that into forge work. Shona is involved with the British Artists Blacksmiths Association (BABA) who do various courses throughout the year and run events to get people together, even from abroad.
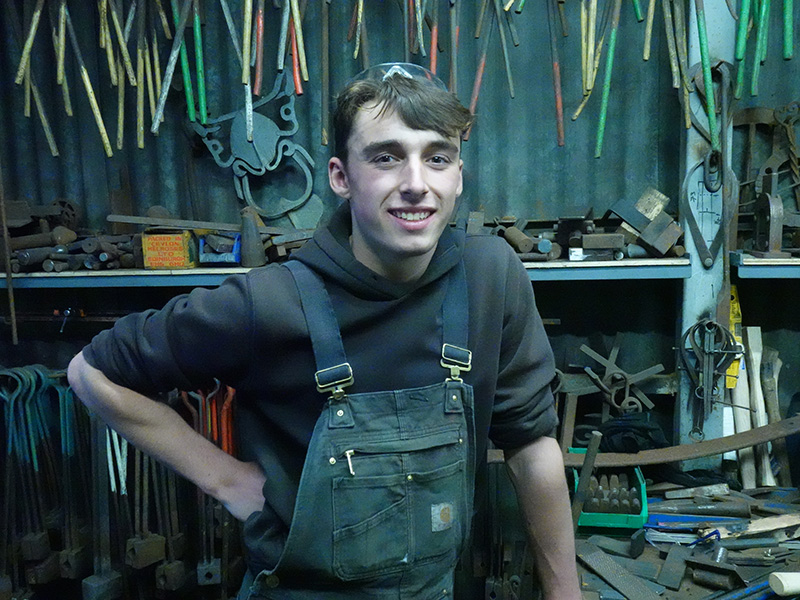
Murray Holmes at Ratho Byres Forge.
Find out more
Find out more about our craft fellowships including how to get in touch if you’re interested in hosting and collaborating on a craft fellowship.
We advertise all craft fellowship, trainee and apprenticeship vacancies on the Historic Environment Scotland Current Vacancies page, when available.
Meet Stacey, a blacksmith based at St Ann’s Maltings in Edinburgh:
Update your personalised ad preferences to view content
About the author:
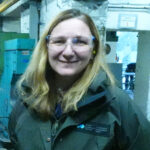
Fiona Kantzidis
Fiona Kantzidis is a Technical Conservation Skills Officer, part of our Trainee and Craft Fellowship Programme, based at the Engine Shed. Fiona has a Post Graduate Diploma in European Urban Conservation from Dundee University, with experience in mentoring and traditional skills provision. Her work on the programme supports the retention of innovative and traditional building skills and involves working with and supporting the development of our Trainees and Craft Fellows.
View all posts by Fiona Kantzidis