Discover four key traditional building skills at the Scottish Crannog Centre’s Iron Age Village
Skills, Vernacular and earth building | Written by: Guest | Monday 10 June 2024
The Scottish Crannog Centre’s Iron Age Village reopened in April 2024. Before its relaunch, we visited Loch Tay to meet our work party of Craft Fellows, who used traditional building skills alongside the centre’s staff to create the village.
In this blog, we share what we learned about some of these skills, including: dry stone walling or dyking, working with round timber and woven wood, turf building and thatching. We also reveal how this unique village is keeping these skills thriving.
Alongside the Scottish Crannog Centre staff and visiting crafts specialists, our work party included Craft Fellows Cat Hotchkiss, Troy Holt, Ross Cameron, and Jack Handscombe. We also spoke to some of the skilled professionals who are passing on their knowledge to those working on the Iron Age buildings.
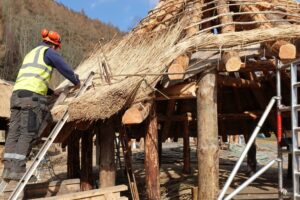
Historic Environment Scotland Vernacular Buildings Craft Fellow Ross Cameron working on reed and straw thatching of the ‘textiles’ hut.
Ancient crafts skills for today
Did you know that crannogs are found in Scotland and Ireland and were usually artificial islands and structures built on lochs and rivers?
The Scottish Crannog Centre on Loch Tay is a visitor attraction and museum with examples of Iron Age buildings and demonstrations of Iron Age life and crafts. It was originally built between 1994 and 1997, and in June of 2021, during a time when plans were being developed to extend the village, its showpiece crannog was lost to fire. Now, the new Iron Age Village offers the opportunity for skilled craftspeople from today to practice, learn and share a range of traditional building skills. The following techniques are just some of the many traditional skills to explore there.
Dry stone walling
The art of dry stone walling is ancient in Scotland, known as drystane dyking, with many of the earliest communities such as Skara Brae, Orkney using this building method. Dry stone walling uses local materials without any mortar between individual stones. The techniques can vary, depending on the size and shape of local stones.
Dry stone walls are essentially two walls, leaning in against each other. In the middle, they are infilled with hearting, also known as ‘fill stones’. Longer ‘through stones’ run through the entire depth of the wall, creating stability, and holding the two walls together. The wall has a slight batter, meaning it leans inwards on both sides. This also means it is wider at the base than at the top.
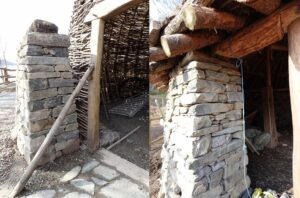
Left: The end of a dry stone wall, part of the roundhouse building before the roof was constructed. Here you can see the slight batter or lean in the wall. Right: The end of a wall, part of the ‘blacksmith’s workshop’ showing the eaves (roof overhang) above.
At the village, we met Jim Doherty, the resident dry stone walling expert. Jim told us that some of the stones come from a local estate and some from near Dunkeld. Large amounts also come from the village site itself, stones that have been washed up by the water of the loch over time.
Jim has been sharing his skills with others at the village including our Vernacular Buildings Craft Fellow, Cat Hotchkiss. Unlike the rest of the HES work party, Cat has been based at the village since November 2023 as part of her HES Craft Fellowship. She has benefited from many mentors including Jim’s knowledge, applying it to some of the village walls and has been building a low stone and turf wall surrounding one of the huts.
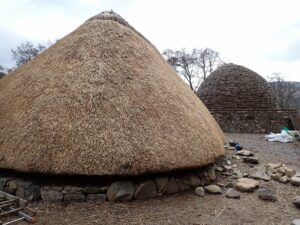
The dry stone wall being built by Craft Fellow Cat Hotchkiss. Here, the challenge is to build it in a very tight space underneath the thatch roof.
Are you interested in learning more about this skill? Find out more about this building technique and how to repair dry stone walls with our Inform Guide: Dry Stone Walls.
Working with round timber and woven wood
The Scottish Crannog Centre holds and displays artefacts and findings from archaeological investigations on Loch Tay. Did you know that archaeology can tell us a lot about how Iron Age communities used wood to build structures?
Today, some considerations have been made regarding modern building standards and practices, such as using modern scaffolding, mechanical tools and lifting equipment.
One of the traditional buildings is a roundhouse made of woven wood (hazel) with a dry stone wall. Turf has been placed on top of the wall and eventually, the building will have a reed thatched roof capped with locally dug clay to protect the ridge. The roundhouse is based on archeological findings at Carn Dubh, Moulin, near Pitlochry.
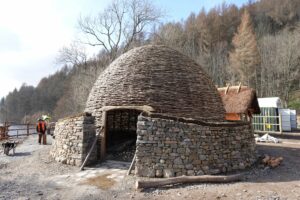
The roundhouse during construction. The top of the dry stone wall is covered with a layer of turf.
There are also the beginnings of a cruck-framed building. Crucks, also known as cuppils or couples, are formed by pairs or sections of wood, making curved timbers, joined at the top to carry the weight of the roof (usually built of timber, turf, and thatch). The village’s cruck uses several types of wood: oak, ash, elm, sycamore, larch, Scots pine and birch to form the two curved frames and the tie beams.
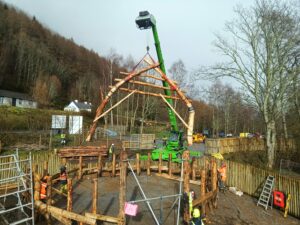
A view of the construction of the cruck-framed building.
The vertical timbers pictured above were charred before being inserted into post-holes. This process removes lignin (a natural binder or polymer), extending the life of the timbers. It also acts to slow their decay and exposure to parasitic fungi by protecting the timbers from ground moisture and rot.
Read more about the characteristics and uses of timber in traditional buildings with our pages about timber and resources about timber building.
Turf building
Turf are rectangular cut blocks of earth and have been used for construction in Scotland throughout history. Traditionally, turf was used for building walls, both as solid turf walls, as infill or as cushioning between stones. Depending on the use, there are thicker blocks (fale), creating building blocks for walls, or thin and long strips (divet), used between stones or turf blocks.
At the village, you can see turf being used at the top of some of the dry stone walls. The turf binds together the top of the wall and provides cushioning for the timber roof structure. In some examples, the turf will be topped with flexible walling materials, such as interwoven sticks, possibly covered with earth to make a wind proof wall.
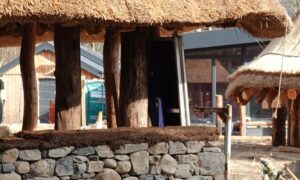
Turf covering the top of a dry stone wall, ahead of planned flexible walling, such as wattle and daub.
The turf was gathered locally, less than two miles away from the village. This makes it a very sustainable building material.
The village has an example of turf being used as a roofing material known as a ‘divet roof’. This uses thin rectangles of turf like you would for roof tiles. This type of roof was also sometimes covered with a layer of thatch or supported by a layer of bark underneath to help make it waterproof.

This is a turf divet roof on the ‘blacksmith’s workshop’, shown during construction.
We also saw a similar type of roof covering being used on the modular modern buildings at the village, a nod to the ancient traditions of turf roofs, though slightly changed. Now, these roofs have a waterproof layer underneath the cover of sedum (leaf succulents).
To find out more about turf, read our publications: TAN 06: Earth Structures and Construction in Scotland and TAN 30: Scottish Turf Construction.
Thatching
Thatching is one of the oldest roofing methods in Scotland and was once very common, but it is now estimated that fewer than 250 thatched buildings remain in the country. Thatching materials such as water reed, wheat reed or straw, heather or marram grass are placed on the roof to help to move water away from the building. At the village, there are several reed and heather thatched buildings.
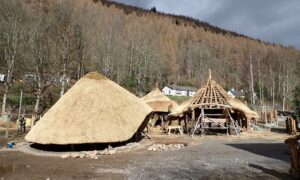
Three of the Iron Age buildings showing reed thatch, during the build.
Our Thatching Craft Fellow, Troy Holt, has been working with Master Thatcher Brian Wilson on many of the village buildings and will be working throughout the Highlands this year. Cat Hotchkiss joined them on the construction elements at the village, and in gathering materials for the build.
The thatching materials have been sourced locally and sustainably. The heather is from community land nearby and the reed is from reedbeds around Loch Tay, in agreement with The Royal Society for the Protection of Birds (RSPB) who manage them.
Did you know harvesting reed for thatching can also support nature as well as building conservation?
Thatching techniques and other traditional building skills are important for continuing to maintain these buildings and the village provides opportunity for skilled craftspeople and professionals to come here to develop and share their skills into the future.
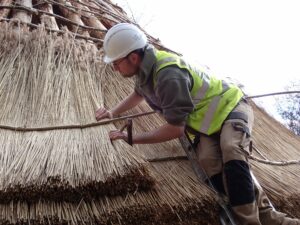
Historic Environment Scotland Stone Carving Craft Fellow Jack Handscombe learned thatching alongside Ross Cameron.
At HES, we have many resources about thatching. Find out more with our pages about thatched roofs and read our publications about thatch.
Find out more
Learn more about traditional building skills and the people that used them at the Scottish Crannog Centre. Our blogs on traditional building skills and materials are great resources to read about the history and modern uses of materials like thatch and timber.
Our free building advice has our latest research and best practice on traditional building materials, components, common defects, and energy efficiency.
Find out more about our Craft Fellowships or get in touch if you’re interested in hosting and collaborating on a Craft Fellowship.
We advertise all Craft Fellowship, Trainee and Apprenticeship vacancies on the Historic Environment Scotland Current Vacancies page, when available.
If you’re considering a career in building conservation or want to develop your skills find out more about building conservation training and skills development or explore our learning opportunities at the Engine Shed.
About the authors
Katie Sludden is a Technical Education Officer, working at the Engine Shed as part of the Technical Outreach and Education team. She loves to develop engaging, inspiring and educational content. See more blogs by Katie.
Anne Schmidt is a Content Officer, working at the Engine Shed. Her background is building conservation and she enjoys telling people about different traditional building materials, particularly lime and sustainable refurbishment. See more blogs by Anne.
About the author:
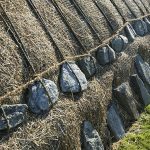
Guest
From time to time we have guest posts from partners, visitors and friends of the Engine Shed.
View all posts by Guest